CAE 解析技術
スムーズな量産移行を促すCAE SYSTEM
山下電気では、CAE SYSTEMを活用し、製品品質の向上と安定量産を行うためにお客様への提案を積極的に行っています。
解析コンセプト
方針
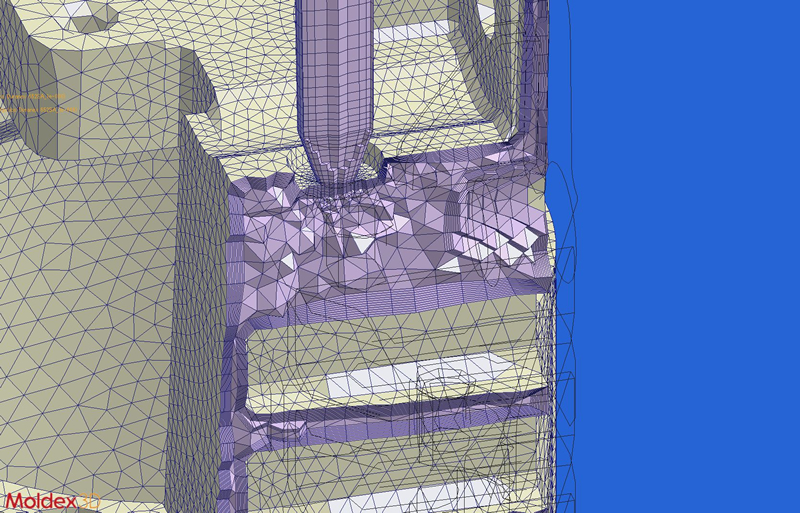
当社が射出成形用CAEを使用する理由は、従来の試作を行って不具合を確認してから金型を修正するのではなく、事前にコンピュータ上で仮想試作を行い、金型を作る前に不具合を解消できるところにあります。
これにより試作後に無理な金型修正を行うことが回避できるため、修正コスト、試作回数、作業時間などが削減でき、要求品質の高い金型でもスケジュールに遅れを出すことなく量産に移行させることが可能になります。
したがって、寸分の狂いの無い解析精度を追い求めるのではなく、限られた時間で金型を量産に移行できるレベルにまとめることがCAE解析の役割と考えています。
実績
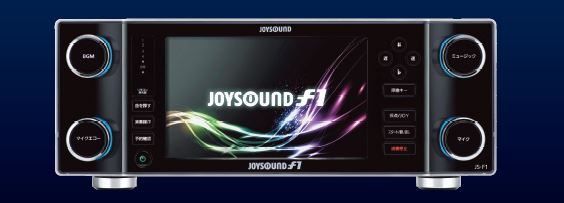
当社の特徴として、CAE解析技術者が成形技術に精通していることが挙げられます。依頼された解析を言われた通りに実行するのではなく、CAEで不足している情報を解析技術者が現実の成形技術で補うことにより、予測精度の高い解析結果を導きます。
これにより、他ではまねのできない金型完成度を現実のものとし、多くのお客様より高い評価を得ています。
業務フロー
金型製作のご依頼後、CAE解析依頼をご依頼ください。
問題点の抽出から対策、試作品のご提示、さらには量産まで対応いたします。
新規金型受注
CAE解析依頼
解析
問題点の抽出(流動性、ウエルド位置、ヒケ、反りなど)
対策
ゲートランナーシステム、成形条件、形状変更、金型構造
試作
T1品質の確保, 金型修正リスクの回避, 短期量産化スケジュール達成
量産
解析ソフトの紹介
解析ソフトの構成
No.1
金型冷却解析
金型冷却システムの最適化。
金型の温度分布の解析に使用します。
No.2
樹脂流動解析
ゲート・ランナーレイアウトの設計を行います。
金型内で溶融樹脂がどのように流れていくのかを解析します。
この段階でウエルドラインの位置・ガス溜り発生の有無がわかります。
充填中の樹脂圧力及び樹脂温度変化などを把握します。
No.3
保圧・冷却解析
体積収縮の確認をします。
ヒケの可能性を判断します。
保圧時の樹脂圧力分布、樹脂温度分布を把握します。
No.4
繊維配向解析
反り解析に必要なデータです。
ガラス繊維やカーボン繊維の配向を解析します。
No.5
残留応力解析
反り解析に必要なデータです。
冷却完了後の残留応力を解析します。
No.6
反り解析
反りの状態を確認します。
No.1~No.5の結果をもとにして反り解析を実行します。
解析結果に問題がある場合、No.1~No.5の見直しまたは成形品形状の変更を検討し、反り量の低減を目指します。
解析ソフト導入履歴
1991年 | 射出成形用CAE「C-MOLD」導入開始。同年流動解析ソフト導入 |
1993年 | 金型冷却解析ソフト導入 |
1995年 | 保圧冷却解析ソフト導入 |
1997年 | 反り解析ソフト導入。流動開始から反りまでが解析可能になる |
2000年 | C-MOLDがMOLDFLOW社に買収される MOLDFLOW社とMPI移行契約を締結 |
2002年 | C-MOLDとMPIの統合版であるMPI 3.0リリース |
2015年 | 3次元CAEソフト Moldex3D導入。C-MOLD最終バージョンを使用中 |
CAE解析事例
Y-HeaT仕様 高輝度パネルの解析例
外観の障害になるウエルドラインやフローマークの改善にCAE解析を導入し ピアノブラック調高輝度塗装レス化を実現させました。
- 主な肉厚:1.5~1.7mm
- 材 質 :PMMA/ABS アロイ材
ウエルドライン位置
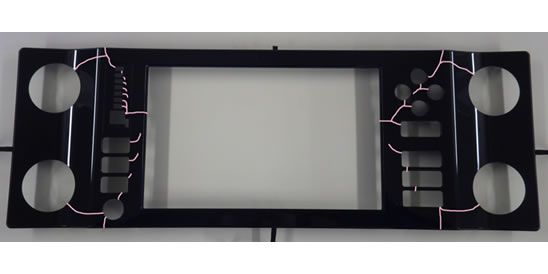
現物のウエルド位置
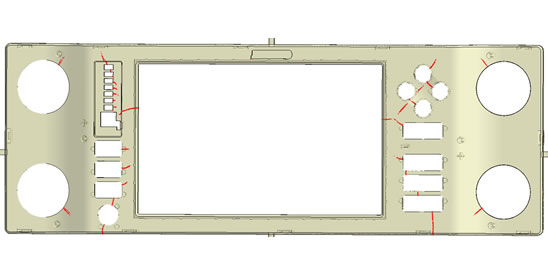
解析のウエルド位置
フローパターン
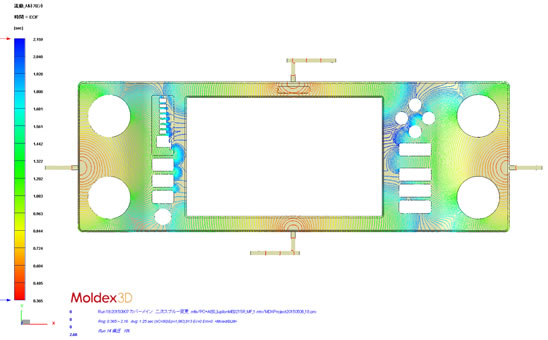
圧力(縦軸0~100Mpa)
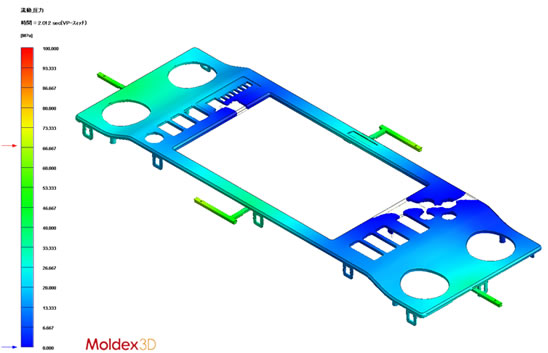
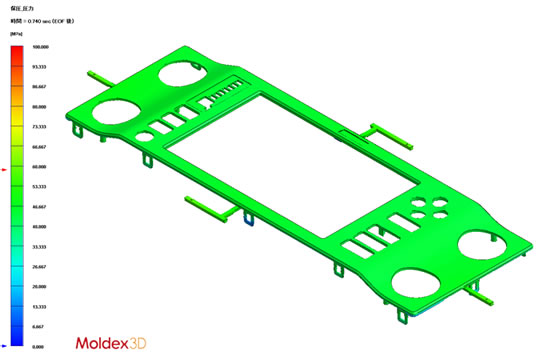
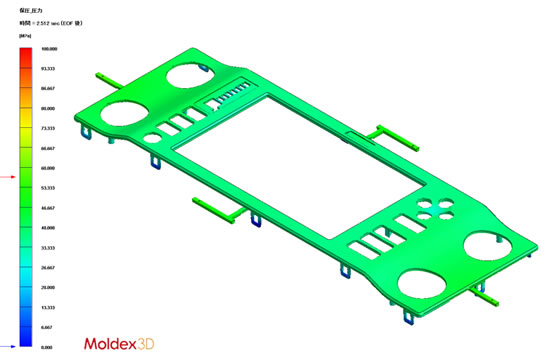
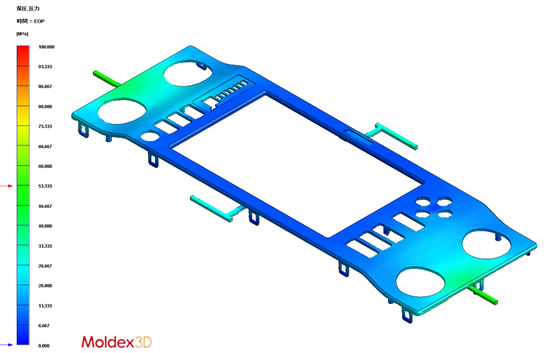
ノートPC用薄肉筐体の解析例
初期の段階で製品にねじれが生じると予測された製品をゲート・ランナーレイアウトの設計及び製品の形状変更で使用可能なレベルに改善しました。
- 主な肉厚:0.9~1.05mm
- 材 質 :PC系アロイ・カーボン繊維入
体積収縮解析結果
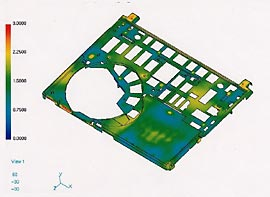
改善前
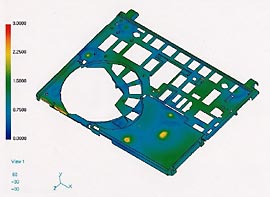
改善後
反り解析結果(解析後変位量5倍)
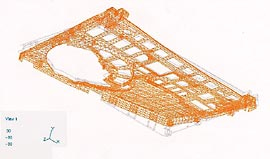
改善前

改善後
CAE SYSTEM Q&A
Q.樹脂の流れは合いますか?
解析対象金型の90%ぐらいは、ほぼ同じになります。残りの10%に関しては、多少のズレを生じますが大きな問題になることは、ほとんどありません。
Q.ヒケは判りますか?
危険性があるか無いか程度の判断はできますが、確立されていません。ヒケは目視による判断になるため、きわどい程度の問題は難しいと思います。
Q.バリは判りますか?
CAEでは、型締力の不足や部分的なオーバーパックに起因するものは予測可能です。金型の問題で発生するバリは当然判りません。
Q.ウエルド位置は判りますか?
フローパターンの表示からフローフロントの合流状態を見て判断できます。但し、ウエルドが見えるか見えないかの外観的な問題は、判断できません。
Q.ガスベントの位置は判りますか?
フローパターンから判ります。
Q.反りは合いますか?
一般的に定性的には合うが定量的には難しいと言われています。当社の場合は、反りの方向はほぼ間違いなく合っています。また、反り量に関しては±0.3mm程度の判定ができます。これは、製品形状、使用樹脂などによって精度が異なるため大まかな目安です。
Q.どのくらい時間がかかりますか?
反り解析まで行うには、1条件で0.5~1時間程度かかります。モデリングと設計を含めたトータルの解析時間は、2日~7日と内容によって幅がありますが、平均で5日(実働)程度になります。ただし、製品の形状変更など設計的な解析の場合は、さらに時間を要します。
Q.ゲートの位置はCAEが決めてくれるのですか?
CAEは、入力した条件で計算を行い、結果を出力するだけです。したがってゲート位置等は解析者が判断することになります。つまり、人間が設計することになります。
Q.金型納期は短縮できますか?
CAEの解析期間は、金型設計と平行して行うことになります。そのため金型の納期短縮には貢献しません。しかし、金型完成後の修正作業が減るため、量産立上げのリードタイムを確実なものにします。
Q.コストダウンに役立っていますか?
目に見える直接的なコストダウンは、なかなか判断が難しいと言えます。ただし不良現象を事前に排除していることから、試作及び量産時の損失を未然に防いでいることで貢献していると考えています。