2色成形における1次2次で異なった表面処理時の考え方
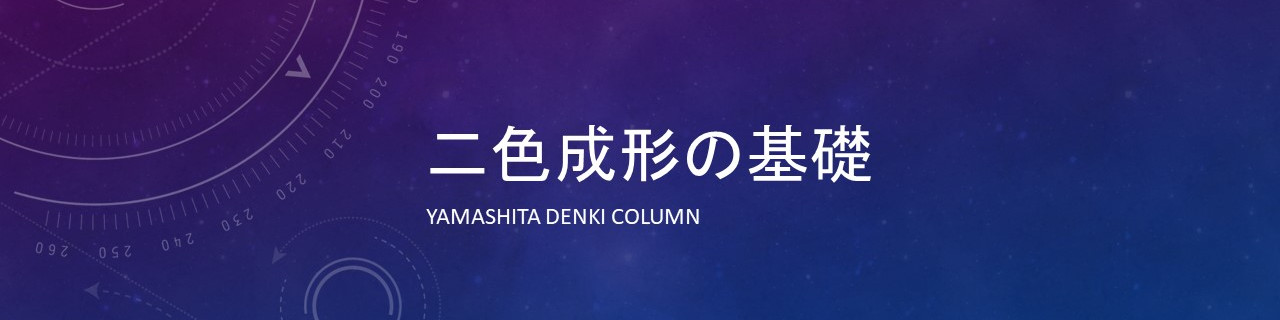
※今回の例の前提は、1次材:PMMA(透明)鏡面/2次材:ABS(黒)シボ とします
1次を成形する時は1次キャビを鏡面に仕上げておきますので特に問題はありません。問題は2次を成形する時で、1次で成形された窓は2次キャビに飛び込んで強く押しつけられます。2次キャビではシボが必要となりますが、当然窓が押し付けられる範囲は鏡面でなければなりませんが一面構成(窓と外観が同一面)のデザインの場合金型上で境界が分からずシボ加工時のマスキング(シボを掛けたくない範囲にテープ等で保護する事)が出来ません。
2色製品で表面処理が1次、2次で異なるケース
(1次透明窓/2次シボ有外観)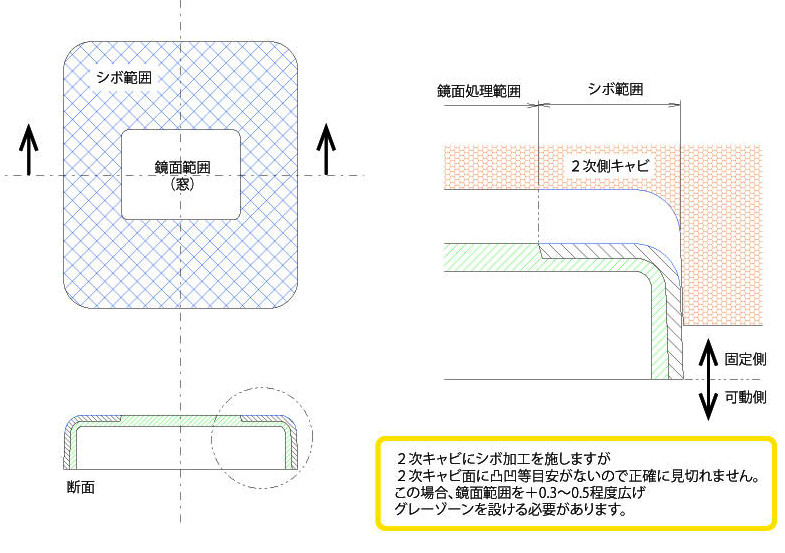
現在ではレーザーマスキング等の技術も発達しておりますが基本的に人の手によってマスキングテープを金型に貼っているのが現状の中で正確に見切る事は非情に困難となります。そこで下記の対策例のようにデザインを若干変更して頂き2次キャビでの見切りをはっきりさせる事が重要となってまいります。
対策例
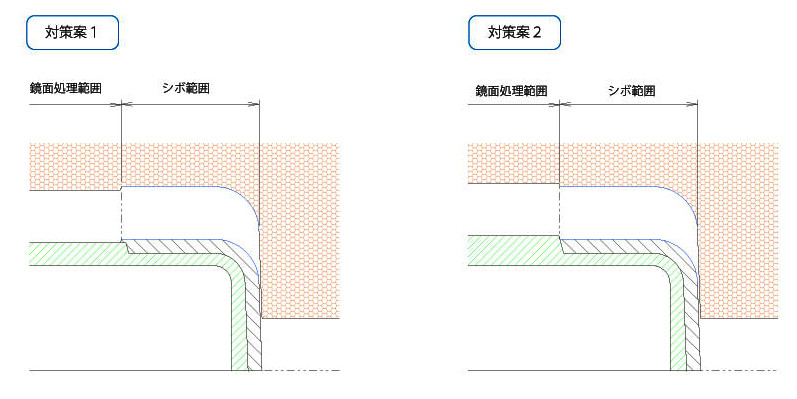
対策案1は1次側を凹ませ2次キャビを凸に、対策案2では1次側を凸にし、2次キャビを凹にしています。
どちらの対策もシボと鏡面の見切りが可能となります。
この対策であれば、マスキング技術による差異も出ず多数個取での再現性も可能です。
今後もこのトピックス内で様々な事例を説明していきますのでご参考にして下さい。
あわせて読みたい記事はこちら
■ 2色成形の材料の組み合わせ■ 山下電気の技術>二色成形
■ 山下電気の技術>金型製作